CTI Marketplace
23-10: 95% Recovery of Cooing Tower Blowdown with an Advance Reverse Osmosis Unit
Regular price
$20.00 USD
Regular price
Sale price
$20.00 USD
Unit price
per
Couldn't load pickup availability
Due to water shortages, increasing regulations and related effluent discharge and makeup water costs, industrial facilities are required to manage their net water consumption in the most efficient way. In many cases, the major water consumer in an industrial facility are the cooling towers, which also produce the majority of wastewater as cooling tower blowdown (CTBD). During the cooling process, the water is significantly concentrated inside the cooling towers (CT), resulting in effluents characterized by high scaling potential caused by Silica, Gypsum, Hardness and Alkalinity, as well as high biofouling potential resulting from the open nature of the cooling towers. The straight-forward way for industrial facilities to save water is to efficiently treat the CTBD and reuse this in the cooling towers as makeup water. However, due to the challenging water composition of the CTBD, conventional membrane technologies are limited in achieving high water recovery. An innovative high recovery membrane-based technology was developed to achieve high recovery of CTBD, and reuse most of this as makeup, thus reducing the Operating Expenditure (OPEX) associated with cooling towers in a process plant. The technology contains a single stage reverse osmosis system, with an integrated salt precipitation unit. This technology operates by recirculating the CTBD through an RO system, followed by a fluidized bed reactor (FBR) in which controlled precipitation of supersaturated sparingly soluble salts is performed. This cyclic process, which occurs in small and controlled intervals, allows for continuous concentration and precipitation of the salts that limit the recovery, without increasing the scaling and biofouling potential seen inside the membranes, thus enabling extremely high recovery rates of up to 98%. The produced by-product solids contain over 90% solids, which leads to easy and cost-effective disposal, without additional sludge minimization or handling processes. This paper presents a case study of a 775m3/day (150 GPM) MaxH2O Desalter commercial unit in an industrial facility in the automotive industry, which is designed to achieve above 95% recovery of the CTBD. The system will be operational in Q1 2023. With conventional technologies, scaling of the membranes would have limited recovery to ~55-60%. At 95% recovery, the theoretical saturation indices (SI) reach LogSI ~3.2 and SiO2 SI ~ 1400%. Achieving such high recovery under the above conditions greatly assist in achieving the zero liquid discharge (ZLD) target by the facility. Due to the substantial costs associated with brine disposal, this solution is expected to reduce OPEX which translates to a very short return of investment (ROI) for the facility.
Materials
Materials
Shipping & Returns
Shipping & Returns
Dimensions
Dimensions
Care Instructions
Care Instructions
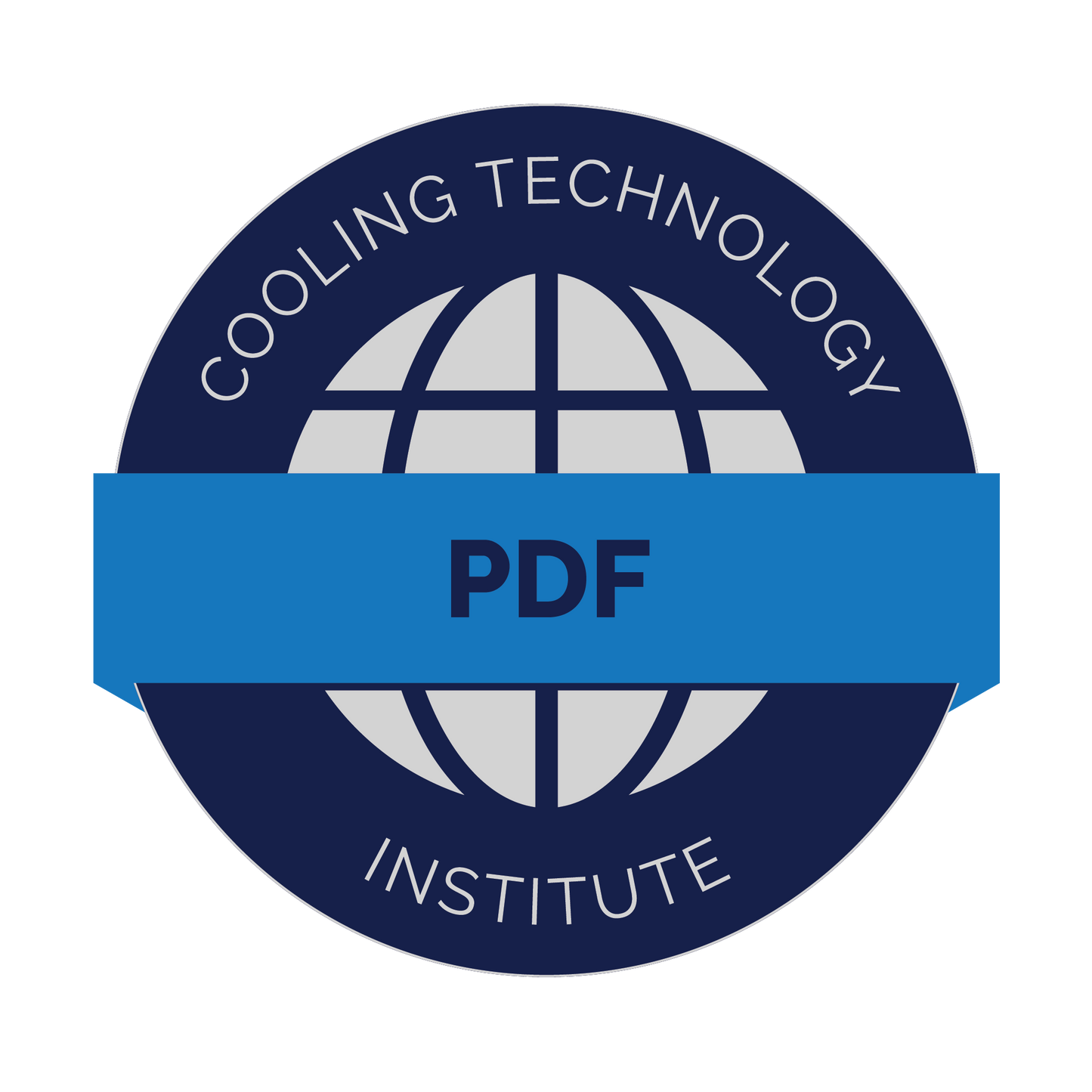
Image with text
Pair text with an image to focus on your chosen product, collection, or blog post. Add details on availability, style, or even provide a review.
-
Free Shipping
Pair text with an image to focus on your chosen product, collection, or blog post. Add details on availability, style, or even provide a review.
-
Hassle-Free Exchanges
Pair text with an image to focus on your chosen product, collection, or blog post. Add details on availability, style, or even provide a review.